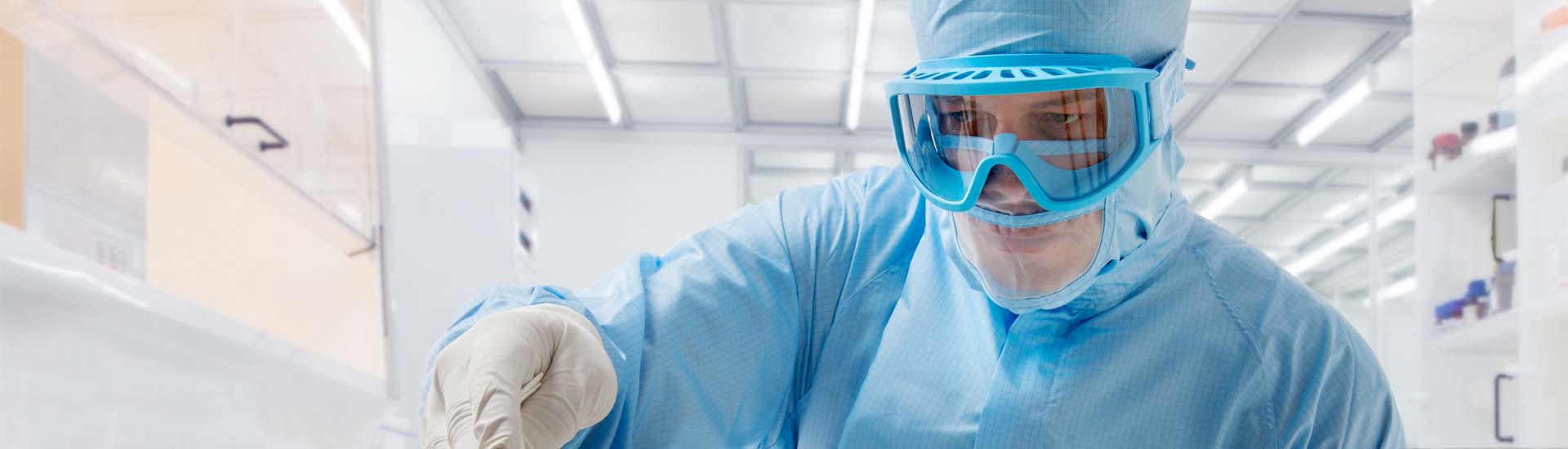
Vileda Professional setting high standards within Controlled environments
Vileda Professional is a world leader in developing, manufacturing and marketing innovative cleaning tools used to clean Controlled Environments . We serve several markets including: cleanrooms in pharma, medical device, laboratories, lab animal research and electronics.
Facilities which are manufacturing products and are adopting a contamination control program now have a resource. We provide complete contamination control solutions incl. planning, trial programs and training. Additional products may be available, please ask us for further support.
With over 20 years’ experience working in compliance with GMP regulations and Cleanroom Standard ISO 14644
We at Vileda Professional have been supporting the CE industry with high-end, unique cleaning tools and methods to make cleaning easier. We offer solutions that help you clean faster and more effectively while lowering your total cost-in-use.
Vileda Professional works closely with leading laundry partners and distributors within the specialized CE industry. As a result, we are close to our customers and able to offer help and advice on site to enable the end-user to get best value-for-money. Both – training and implementation on site - are part of our service.
Please feel free to have a look at our TRAINING CLIPS.
ISO - International Organization for Standardization
Cleanrooms are classified according to the cleanliness level of the air inside. The cleanroom class is the level of cleanliness the room complies with, according to quantity and size of particles related to volume of air.
The guiding worldwide classification system is part of ISO 14644-1. This standard includes the cleanroom classes from ISO 1 up to ISO 9, with ISO 1 allowing the least particles.
The old Federal Standard 209 (class 100,000; 10,000; 1,000; 100; 10; 1) was withdrawn in 2001 and officially replaced by ISO 14644-1, but it is still widely used. In addition, cleanrooms must also comply with industry-specific and even regional standards. For example, EU GMP (A-B-C-D) applies to pharmaceutical manufacturing and USP (795, 797 and 800) to compounding pharmacies.
GMP - Good Manufacturing Practices
Annex 1 Revision: Manufacture of Sterile Medicinal Products
EU GMP Annex 1 is the primary document governing the manufacture, control and release of sterile pharmaceutical products (both terminally sterilised and aseptically filled medicines). The Annex will shortly undergo a comprehensive update, as signalled by a new draft issued in February 2020.
Disinfection:
The Annex 1 Draft version states that the disinfection of clean areas is particularly important. They should be cleaned and disinfected thoroughly in accordance with a written program. For disinfection to be effective, cleaning to remove surface contamination must be performed first.
Cleaning programs should be effective in the removal of disinfectant residues. Disinfectants and detergents should be monitored for microbial contamination. Disinfection dilutions should be kept in previously cleaned containers and should only be stored for defined
periods.
Equipment:
The Annex 1 Draft version points out that the cleaning process should be validated so that it can be demonstrated that it:
- Can remove any residues that would otherwise create a barrier between the sterilizing agent and the equipment surfaces.
- Prevents chemical and particulate contamination of the product during the process and prior to disinfection.
All critical surfaces that come into direct contact with sterile materials should be sterile.
ESD - Electrostatic Discharge
Electrostatic discharge (ESD) is the sudden flow of electricity between two electrically charged objects caused by contact, an electrical short, or dielectric breakdown.
A build-up of static electricity can be caused by tribocharging or by electrostatic induction. The ESD occurs when differently-charged objects are brought close together or when the dielectric between them breaks down, often creating a visible spark.
ESD can cause harmful effects including explosions in gas, fuel vapor and coal dust, as well as failure of solid state electronics components such as integrated circuits. These can suffer permanent damage when subjected to high voltages.
Electronics manufacturers therefore establish electrostatic protective areas free of static, using measures to prevent charging, such as avoiding highly charging materials and measures to remove static such as grounding human workers, providing antistatic devices, and controlling humidity.
We know the challenge in the different standards and classifications
Our products and systems have been designed to address the various challenges. To ensure same high quality level every time, all our products and systems have been qualified and validated to fully comply with industry standards and recommended practices. Please ask for our documentation - CLICK HERE TO GET IN CONTACT WITH US.